Colour your environment
Vases for all tastes
Small ideas for the home or as gifts
Everything for a perfect table
Our plates
Tasty breaks
Unique creations for your special moments
With you even at the beach!
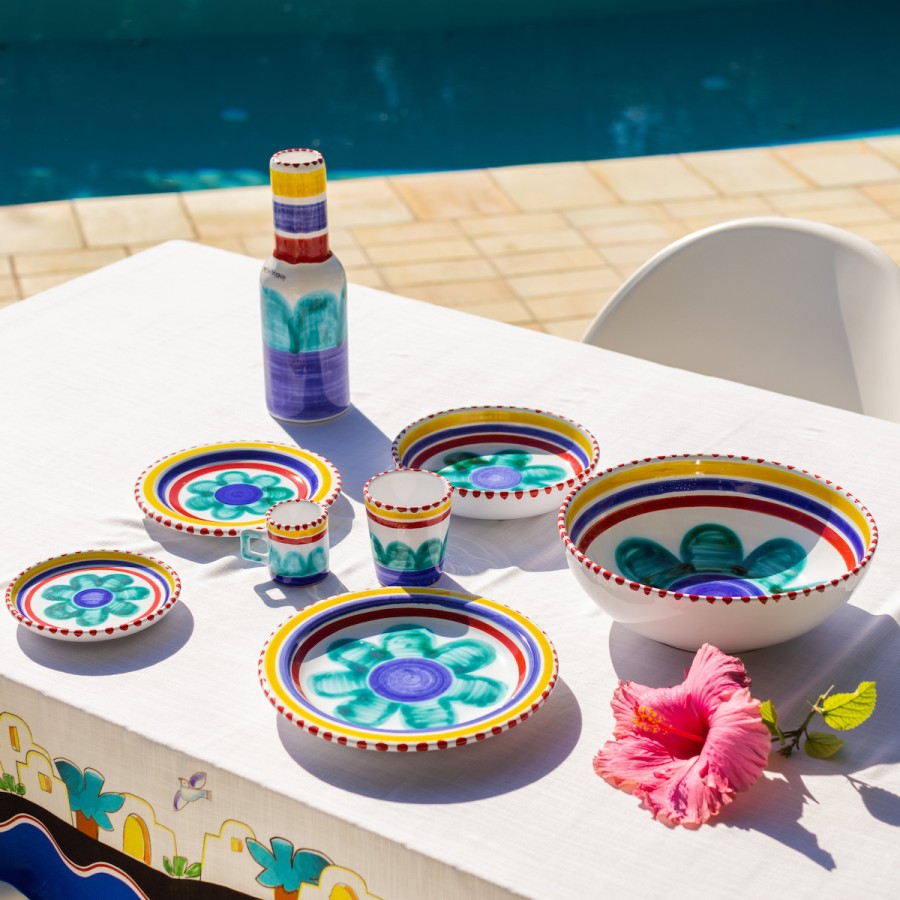
Mangiallegro
More than 30 mood-inspired decorations to adorn your table and kitchen; sets of plates, coffee cups, glasses, appetisers, bowls and more!
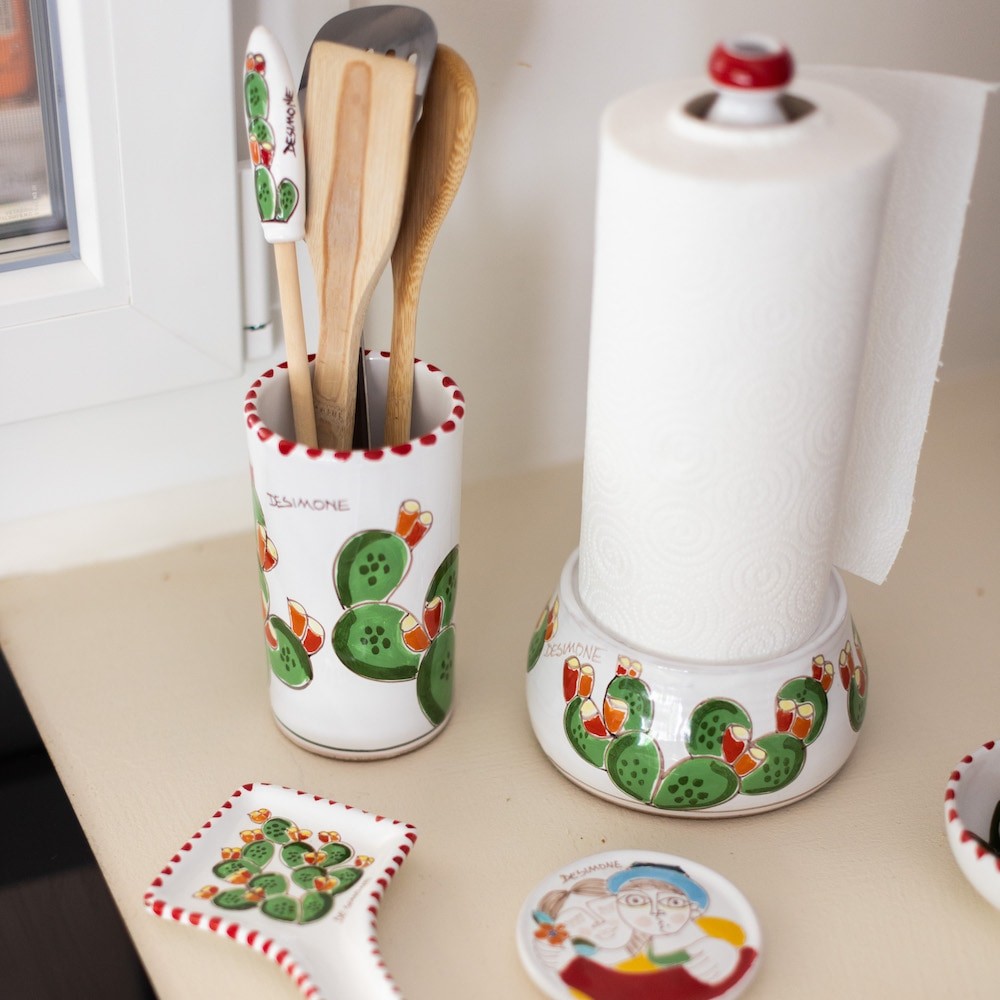
Folk
A whole world to discover when it comes to folklore, as the fantasies in this line demonstrate, which tell the story of the traditions of Sicily.
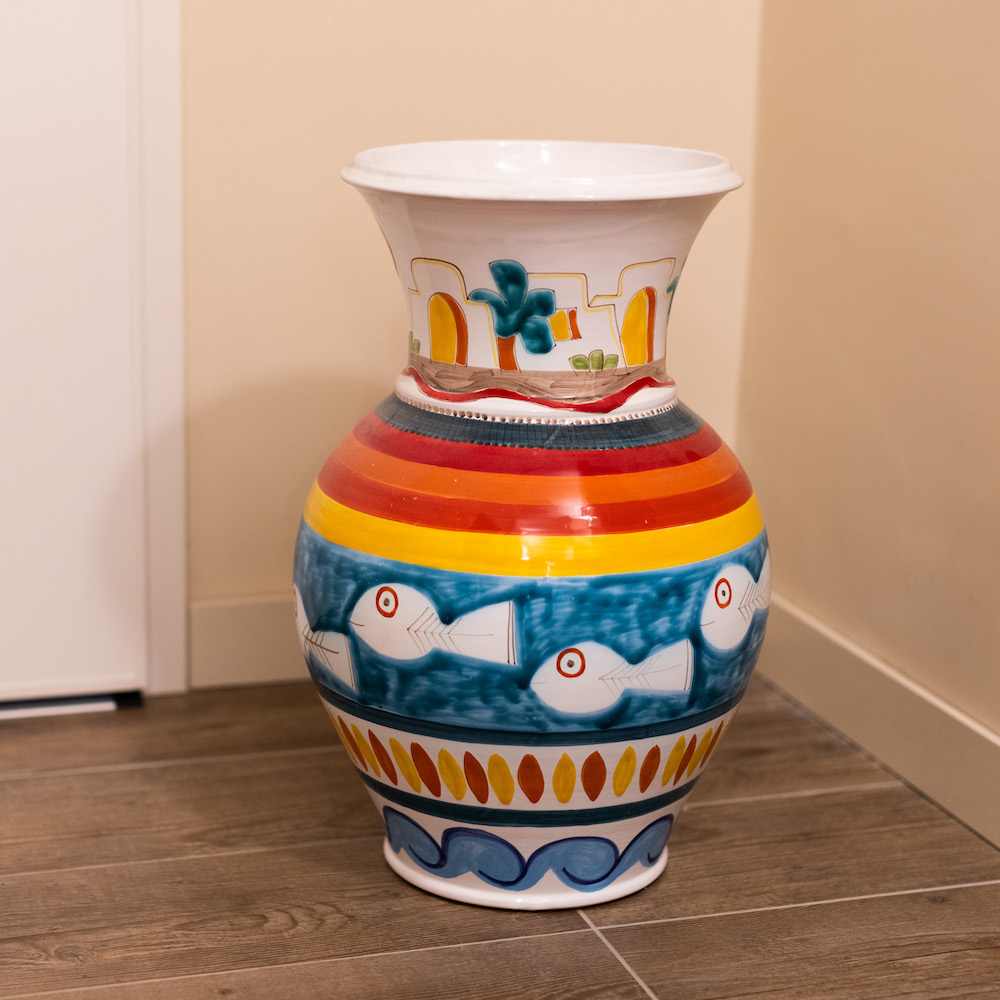
DS
Extraordinary creations where the attention to detail is maniacal, with scenes rich in nuances and elements in the original De Simone artistic style.
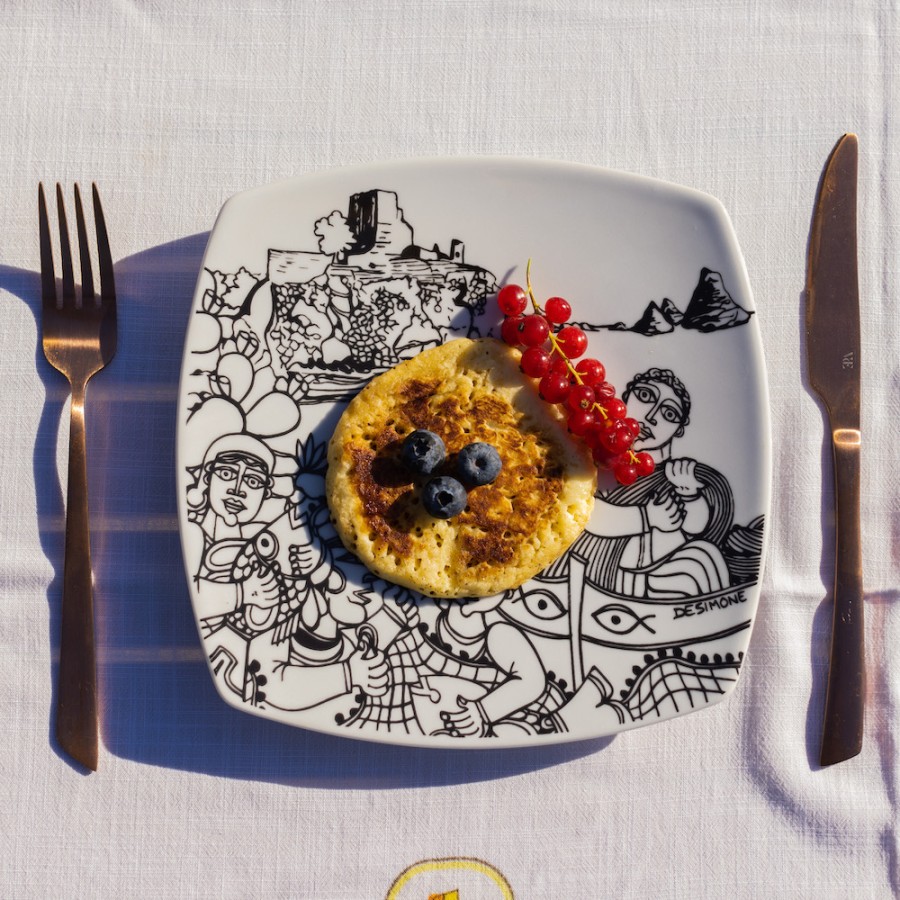
Bianco e Nero
Characterised by the essentiality of its colours and the use of porcelain, ideal for heat resistance.
Discover our workshops and learn how to work with ceramics
Spend a day of craftsmanship at the Ceramiche De Simone workshop. It will not be a simple visit but a real plunge into the Sicilian tradition, where ceramic work has a centuries-old history.
You will visit the workshop, discover all the secrets hidden behind the ancient Sicilian art of pottery making, make your own pottery together with our craftsmen, and can purchase our creations on site if you wish to take souvenirs with you.
Buy your exclusive experience online or give it as a gift to the people you love! It can be a great idea to do something different with your sweetheart or children. We are sure you will enjoy it and you will always have something to remind you of the day you spent together.
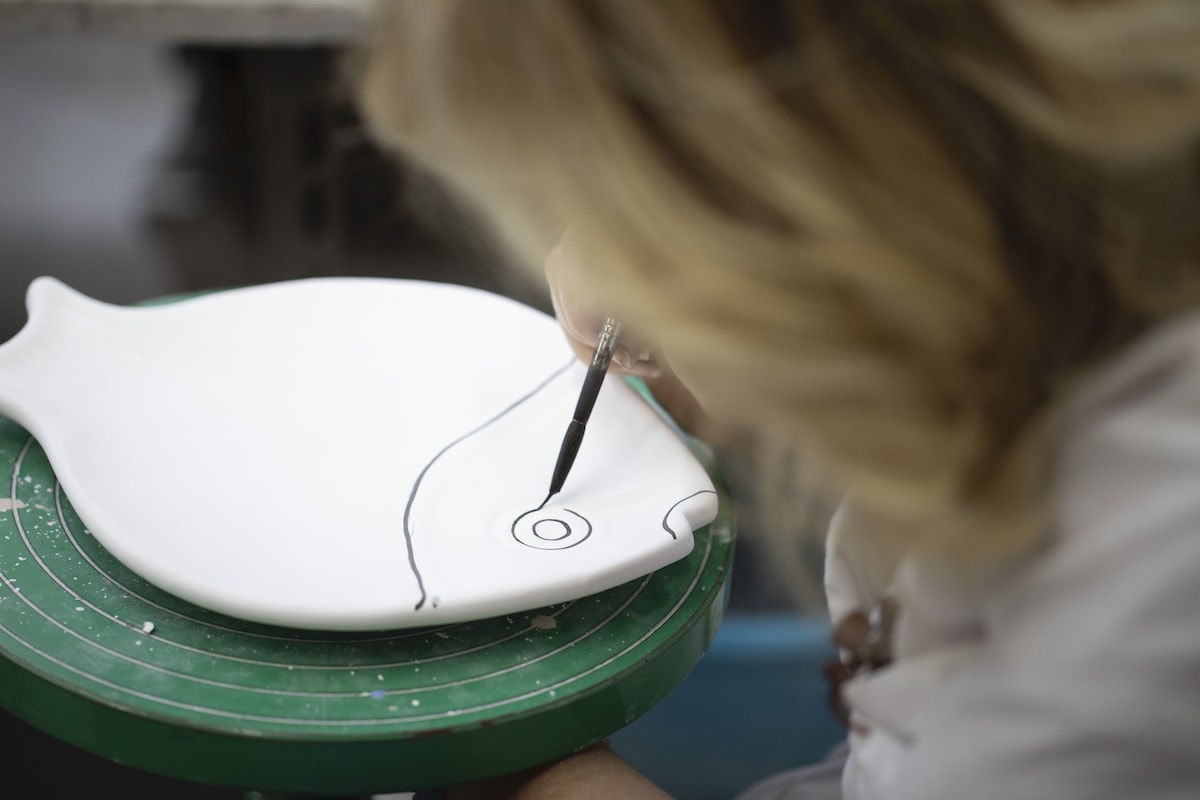
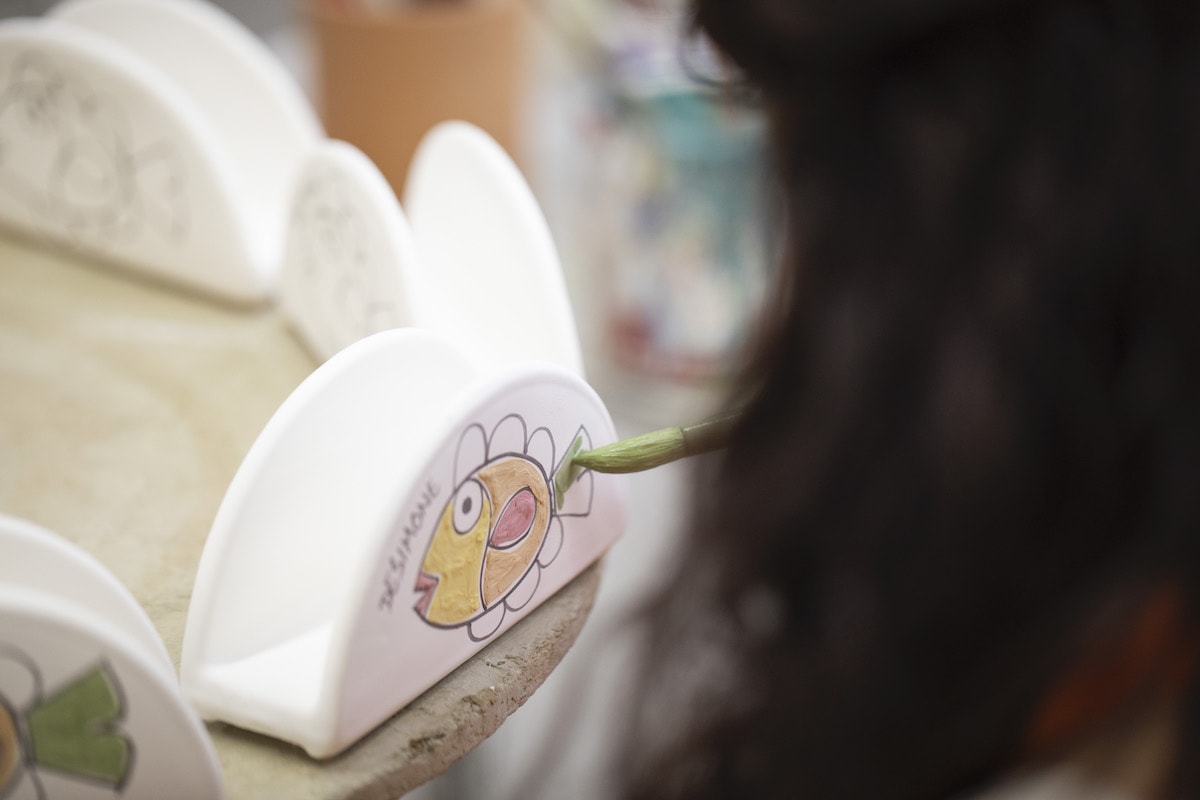
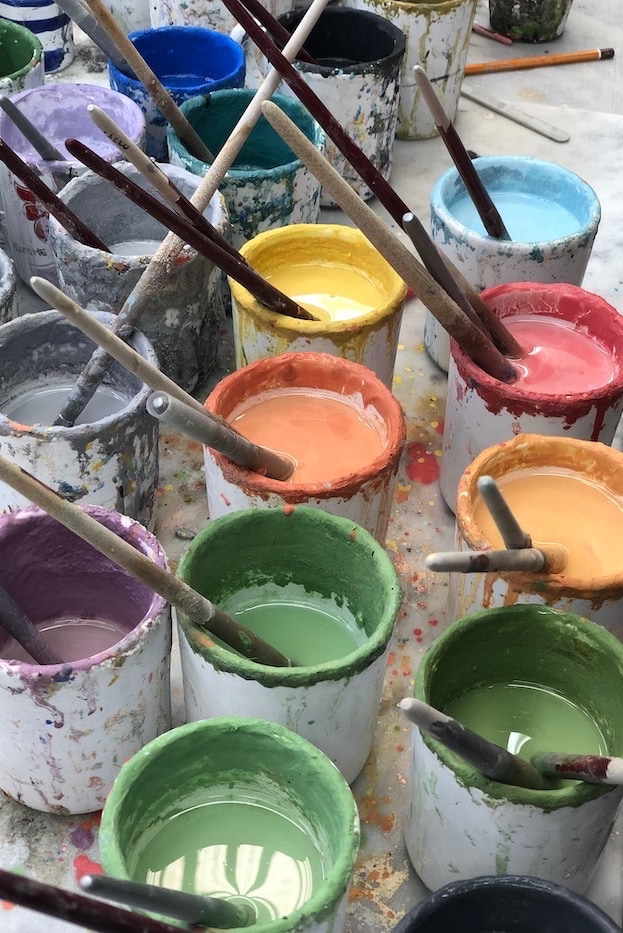
Manufacturing
The quality, the lively colours and the attention to details are the distinctive features of this brand that make each Ceramiche De Simone masterpiece a unique and inimitable piece.
Modelling with the potter's wheel
The potter puts the clay into the centre of the turntable and keeps wetting it as it turns. Then, by using his fingers, he molds the walls of the object from the bottom upwards into the desired form. Utensils help give the finishing touches to the shape, and finally the object is lifted away from the wheel with a steel cable.
After a brief drying out period, the clay reaches the required hard leather consistency, which allows it to be finished off and possibly engraved. Now, the handles and other parts can be attached because the clay is hard enough, although it still retains a certain level of plasticity.
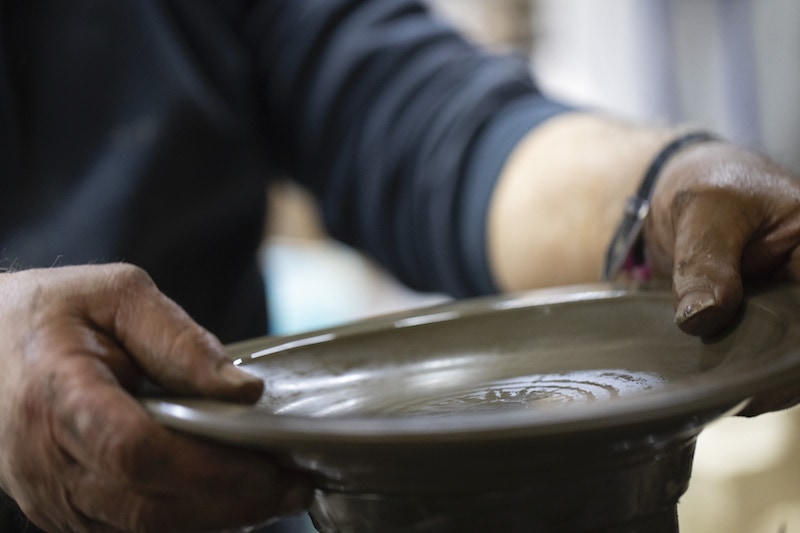
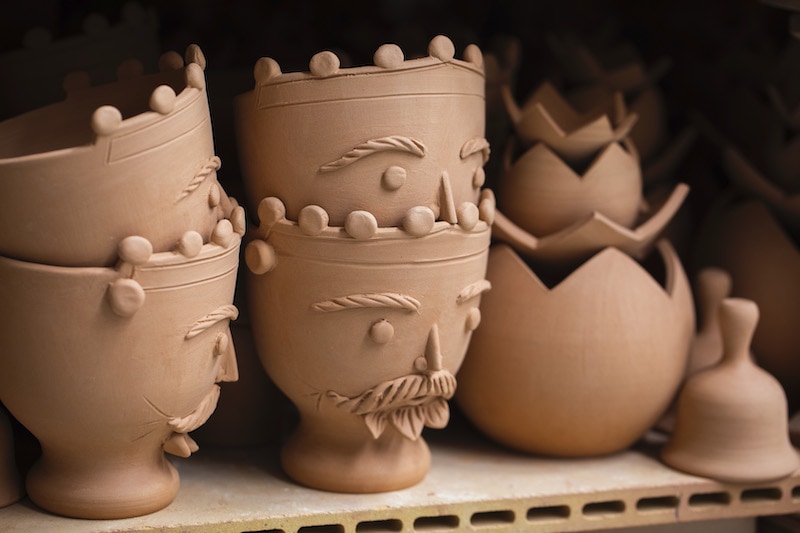
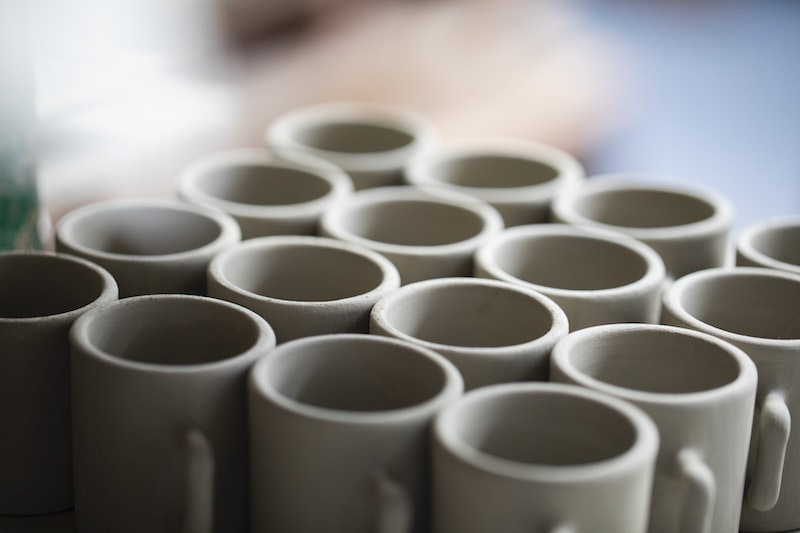

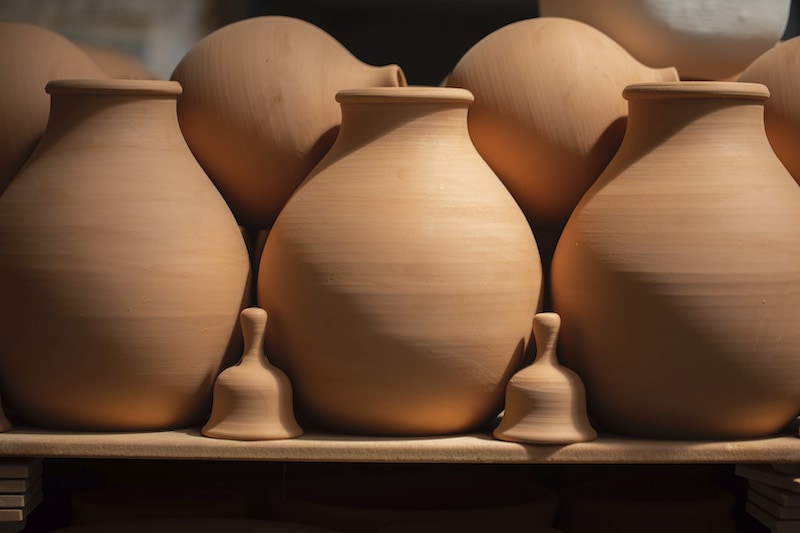
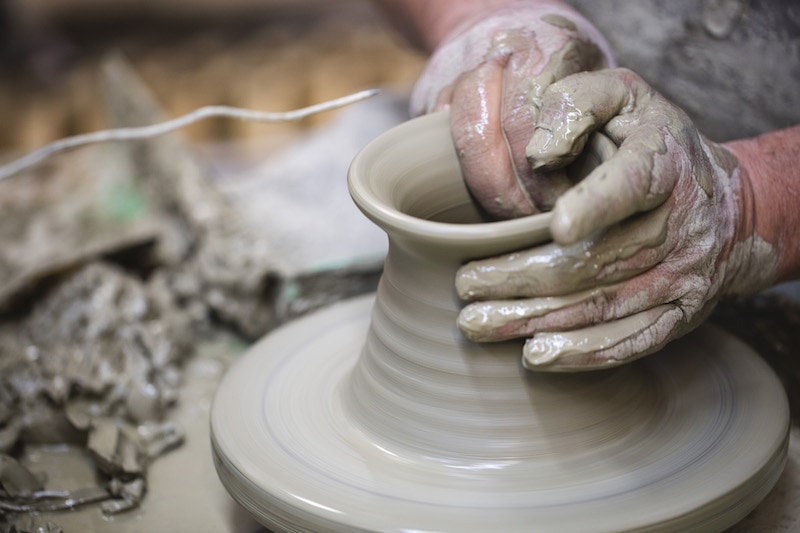
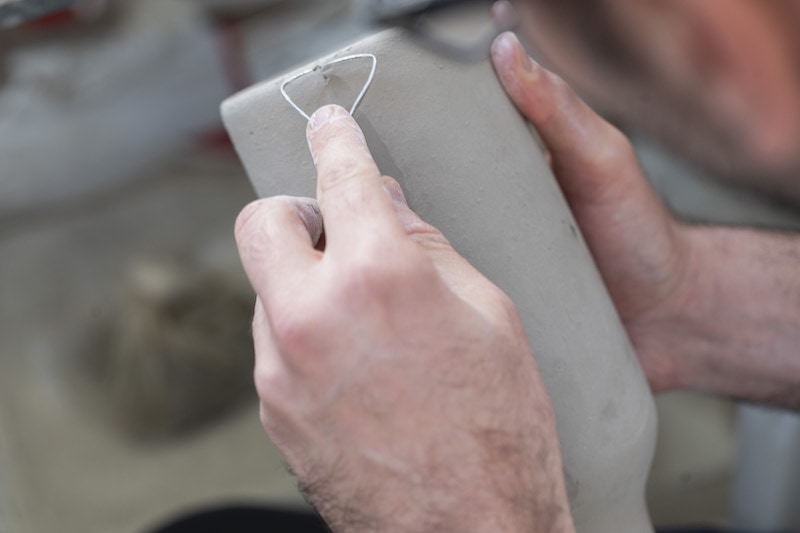
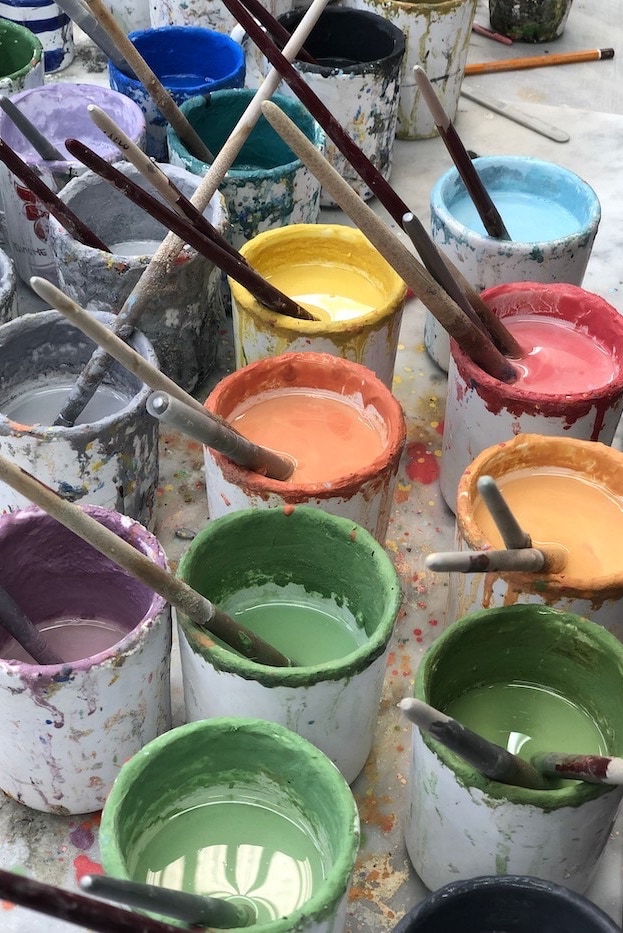
Modelling with molds
This method requires a mold that replicates the object that is to be reproduced.
The clay is pressed manually into the shape and after a period of time it is lifted away from the mold and is finished by hand.
The pressing technique
This method requires a hydraulic clay or rotary press, in which printing matrixes are placed, one male and one female, which when joined together press the clay between them and create the typical De Simone shapes.
After the modelling process with the wheel, the mold or the press, the object is exposed to the air so that it can dry out naturally and become accustomed to the humidity level, which also helps it to reach the required level of plasticity.
The terracotta becomes a reddish colour due to the presence of iron oxide and salt, which occurs when the clay is baked in huge ovens at around 960°C. The object is immersed in a glaze that covers it with a white layer, which serves as a base for the decoration.
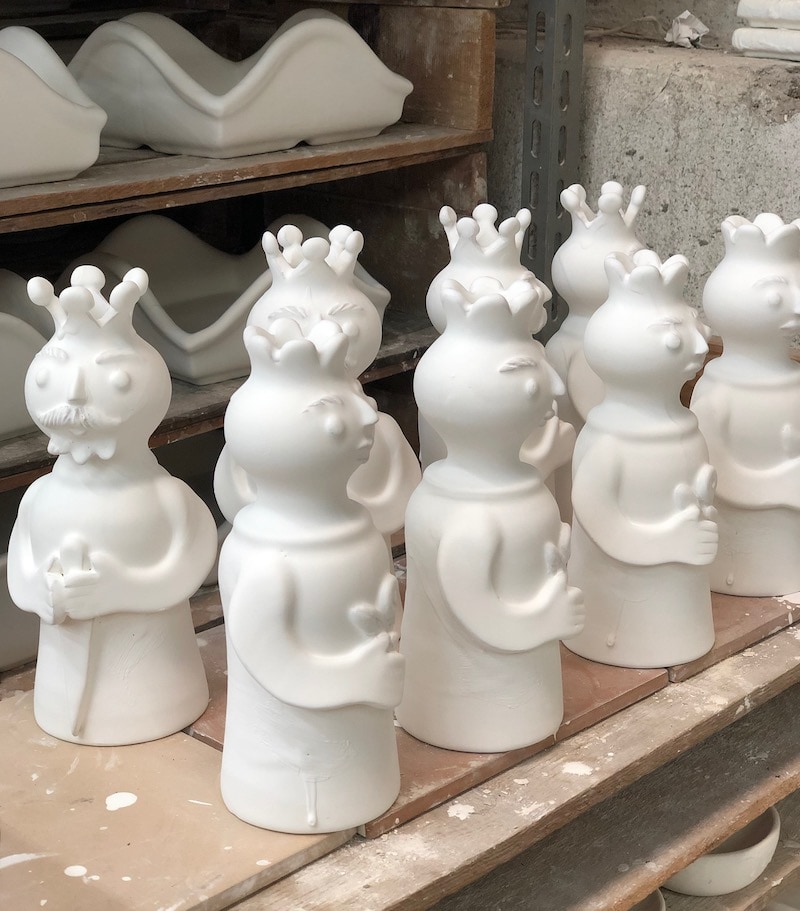
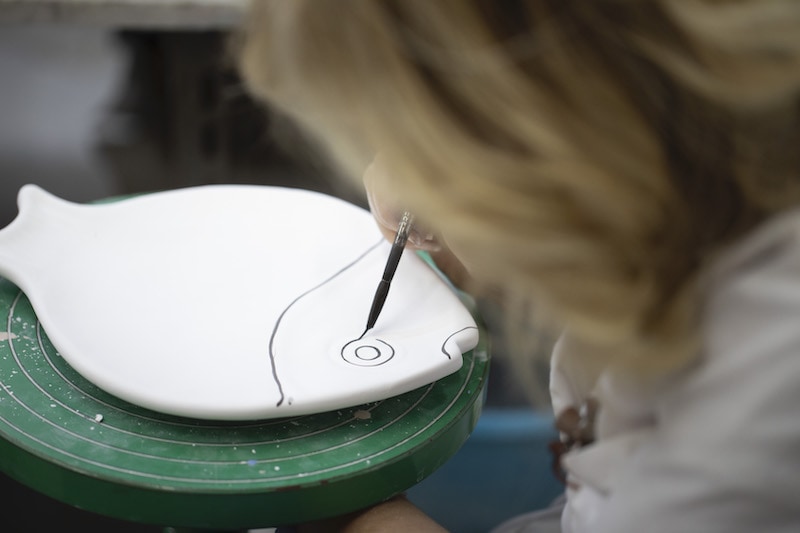
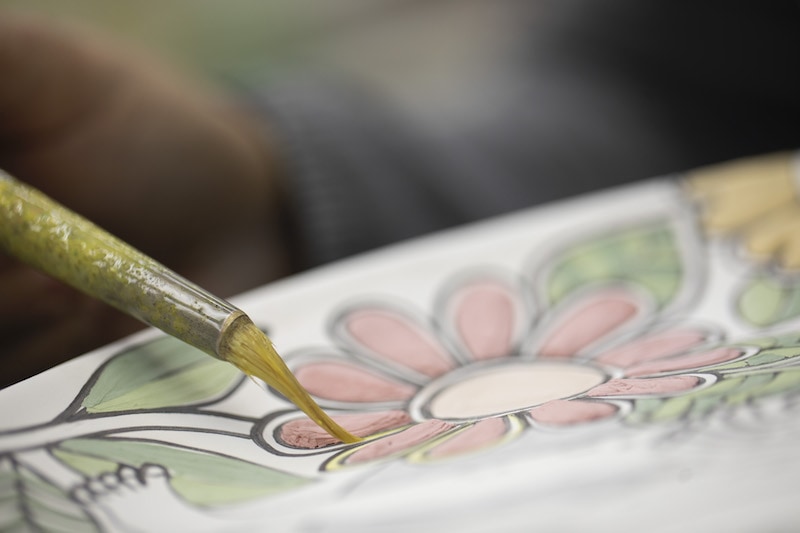
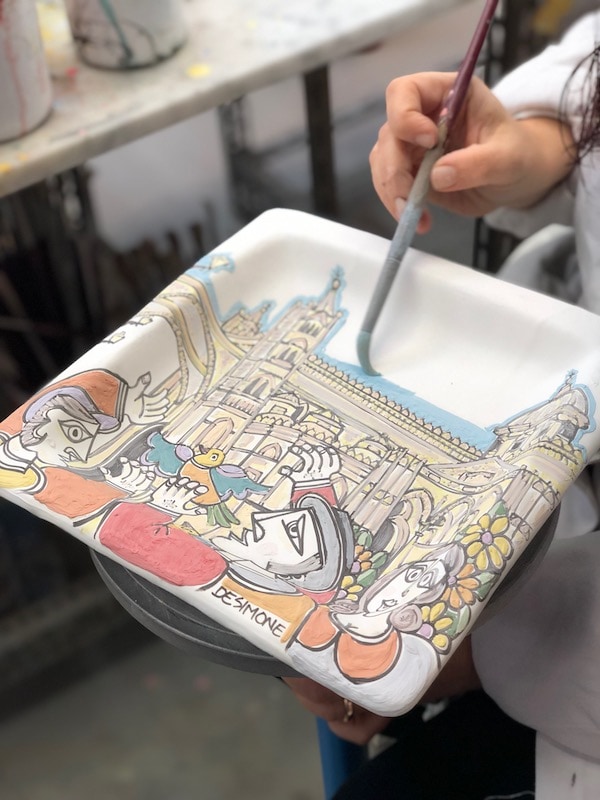
The decoration
The decorating phase is the moment when a blanket of colours explode and bring to life an inexhaustible variety of scenes. This unfolds a multicoloured parade of mermaids and paladins, farmers and sailors carrying out traditional activities, musical bands and town festivals, all rigorously produced by hand using unleaded colours.
After the glazing and decorating, the objects are baked in the oven for a second time at about 900°C, which permanently fixes the glaze and gives the ceramic its typical resistance and shine.
White clay
The handmade articles in white clay are the best in our collection, characterized by the lightness and fineness of the mixture, which can be compared to porcelain. The white paste is a well-known mix of clay and water, which is used in its liquid state and poured into a plaster mold. The plaster absorbs the water and draws in the clay, which solidifies onto the inside walls of the mold forming a thickness that gradually increases. When the thickness has reached its full capacity and the excess liquid is tipped out of the mold, the desired piece is ready. The next stage is identical to the red clay process: finishing, baking, glazing, decorating and final baking.